US +1 908 782 5800 | UK & Rest of World +44 (0) 330 822 6000
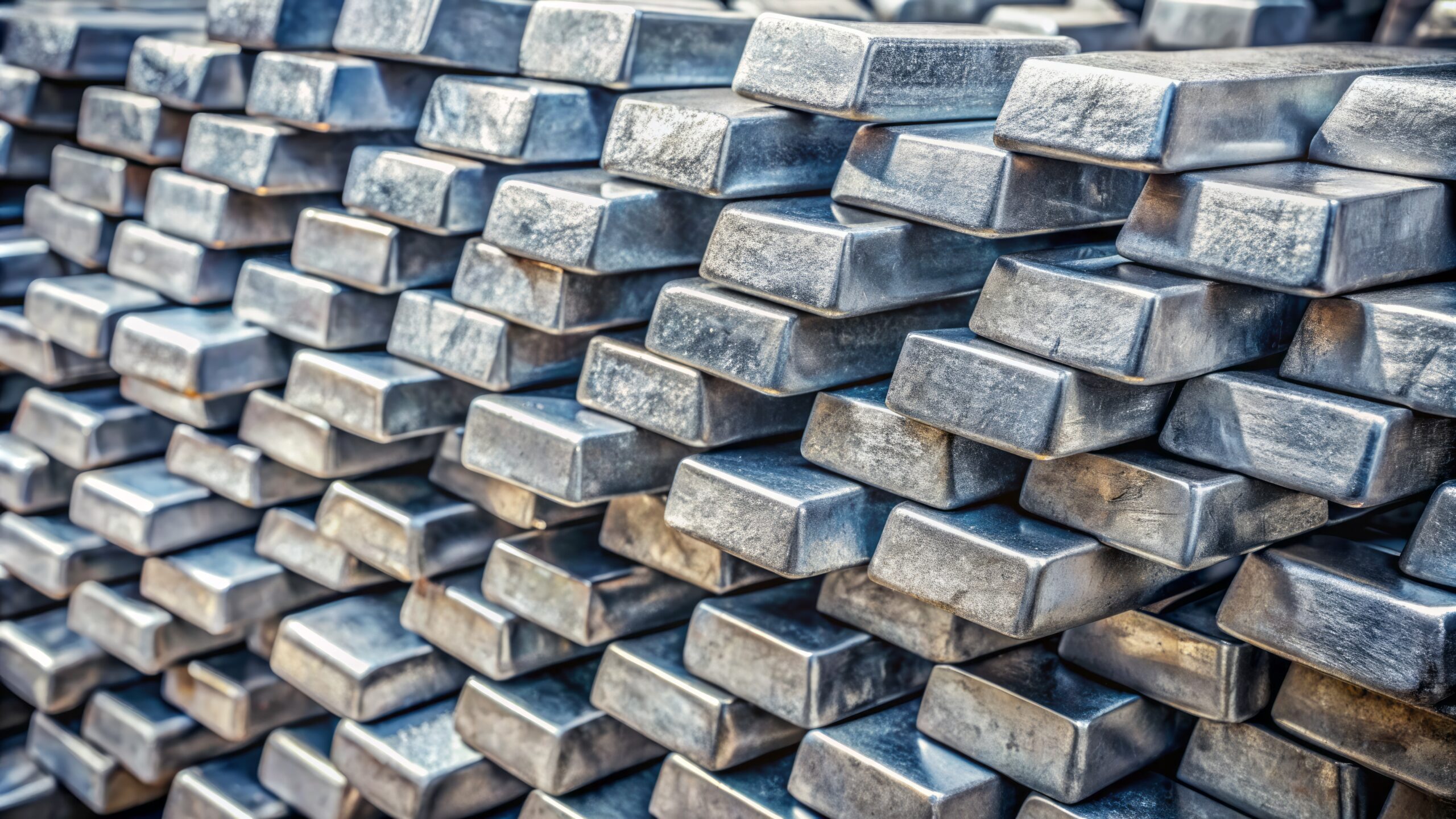
Elektron® 21 Sand Casting Ingot
Our flagship high-strength, heat-treatable magnesium based casting alloy.
For use at temperatures up to 200˚C, this alloy has excellent corrosion resistance characteristics and castability, making it the suitable material for a range of aerospace applications.
Product Information
Find out more about this product below.
Support and downloads
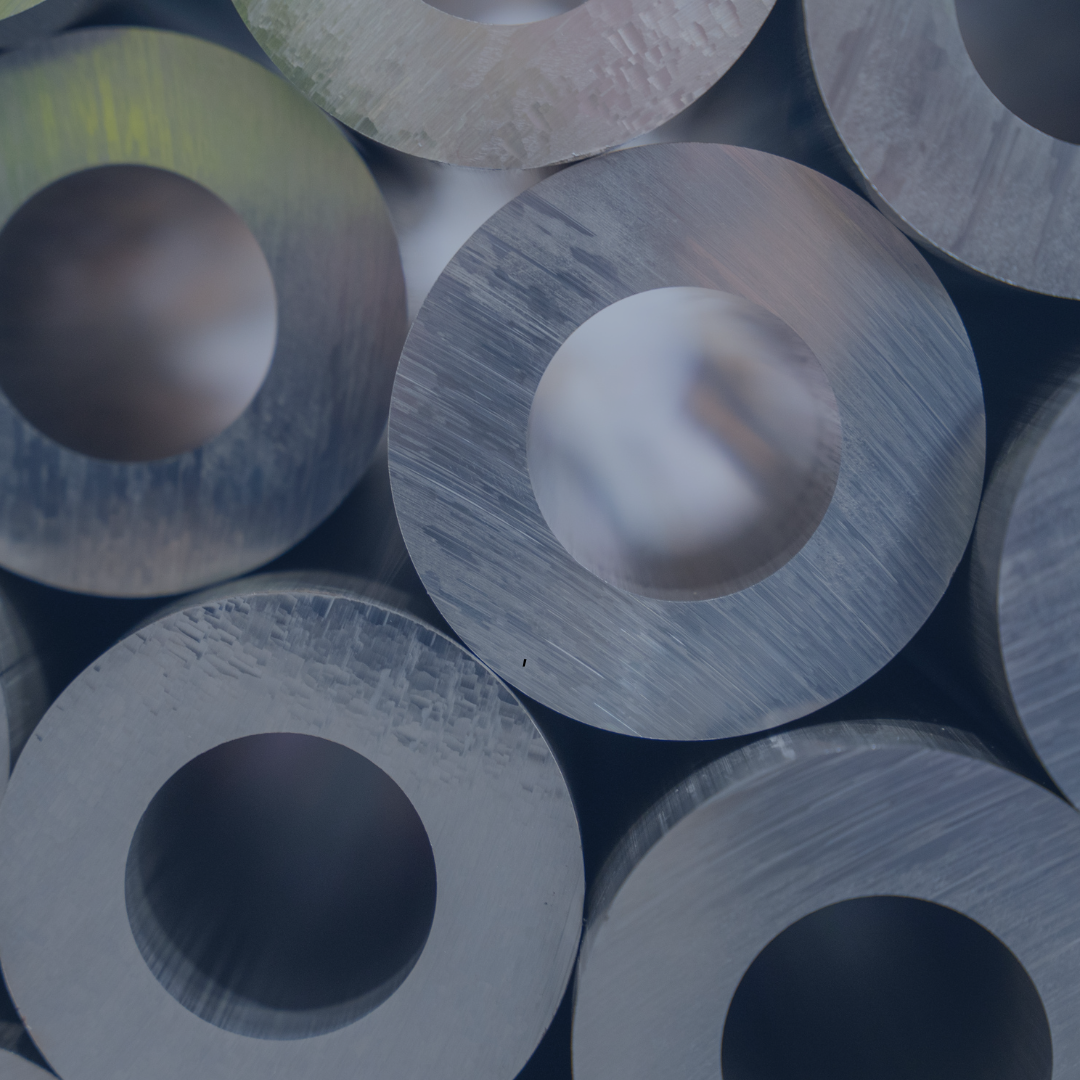
Make an enquiry
Please fill in this form to contact us for sales, support or general enquiries. Thank you.