US +1 908 782 5800 | UK & Rest of World +44 (0) 330 822 6000
In aerospace engineering, the drive for more lightweight, durable, and efficiently manufactured materials is relentless. Luxfer MEL Technologies is leading this journey, crafting innovative solutions that are shaping the future of aerospace components.
The Dialogue of Innovation
At a recent engagement, Paul Lyon FIMMM of the IOM3 Non-Ferrous & Light Metals Group Leadership Team, and Prem Mahendran of Luxfer MEL Technologies, examined the intricacies of magnesium alloy development. Their conversation underscored a crucial industry consensus: innovation within the aerospace sector hinges on the development of materials that are not only lightweight and robust but also produced through streamlined, efficient processes.
Navigating Challenges
The aerospace industry is navigating several challenges—from the imperative of decarbonisation to the aftermath of supply chain disruptions triggered by the COVID-19 pandemic. The Paris Air Show in June 2023 spotlighted these challenges, revealing the underlying issue of protracted lead times in delivering essential aircraft components—an issue that persists despite the easing of pandemic-related disruptions.
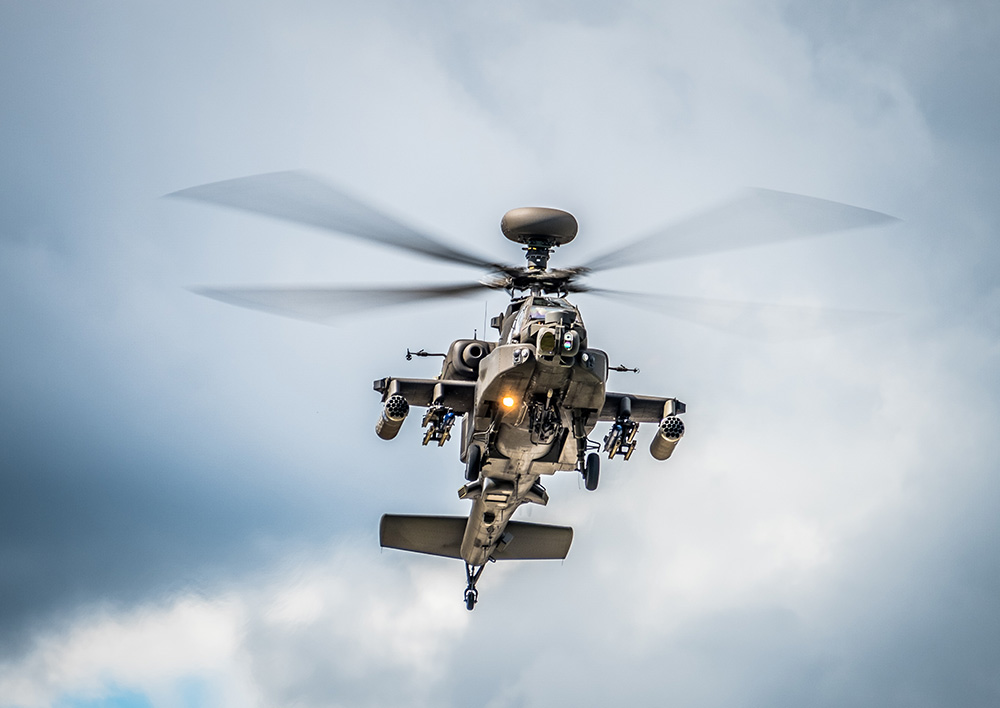
The Elektron® 21 Paradigm
A prime exemplar of this innovation is Luxfer MEL Technologies’ Elektron®21 product, a magnesium alloy that’s applications within the aerospacesector are profound. Utilised by many OEMs, its applications range from magnesium castings to direct chill cast scenarios, embodying the essence of cutting-edge material application in aerospace.
Transforming Material Production in Aerospace Applications
Luxfer MEL Technologies has been instrumental in addressing these challenges. The UK-based division has pioneered an alloy-specific manufacturing route, significantly curtailing the lead times for producing lightweight components—a transformative step that can reduce production timelines.
The Magnesium Advantage
Magnesium stands out as the lightest structural metal, offering an exceptional strength-to-weight ratio for weight-sensitive applications. The development of Luxfer MEL Technolgies’ Elektron® Magnesium alloys, known for their self-extinguishing properties and flame resistance, supportsthe material’s potential in aerospace applications, particularly in sand castings for new build programs.
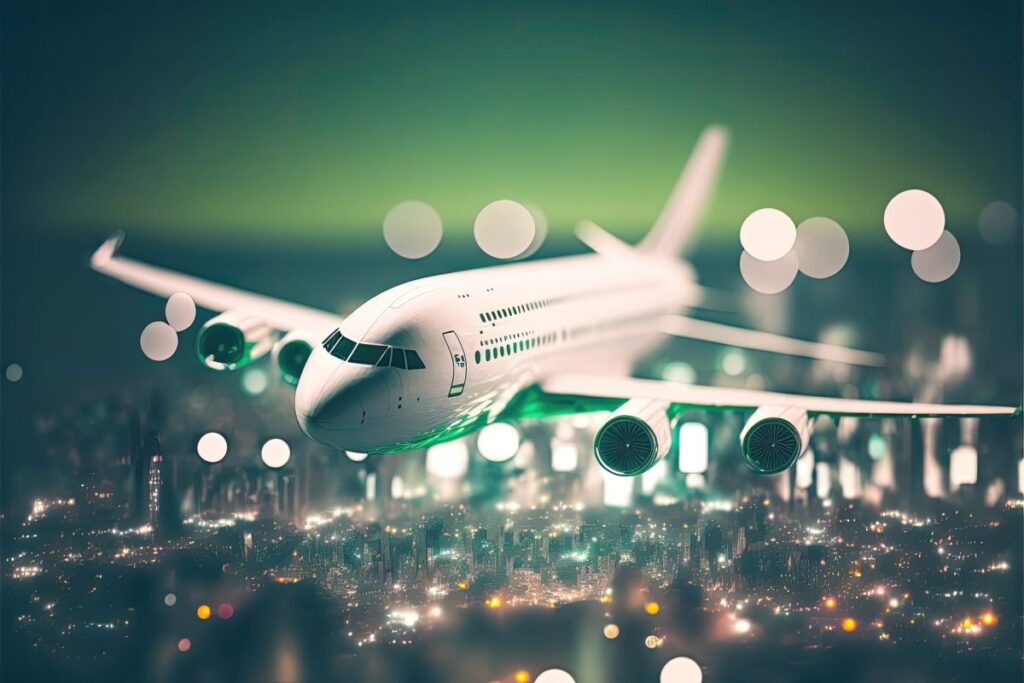
Enhancing Manufacturing Efficiency
Luxfer MEL Technologies has innovated by machining components directly from large direct chill (DC) cast slabs, maintaining the mechanical properties synonymous with established sand-cast alloys. This process not only streamlines manufacturing but also opens avenues for rapid prototyping and the expedited production of aerospace components.
A Vision of Interchangeability
The goal is clear: achieving specification properties in DC cast slabs that align with those of established sand-cast alloys. This approach minimises the risks associated with changing manufacturing routes and fosters interchangeability between castings and machined-from-solid slab components.
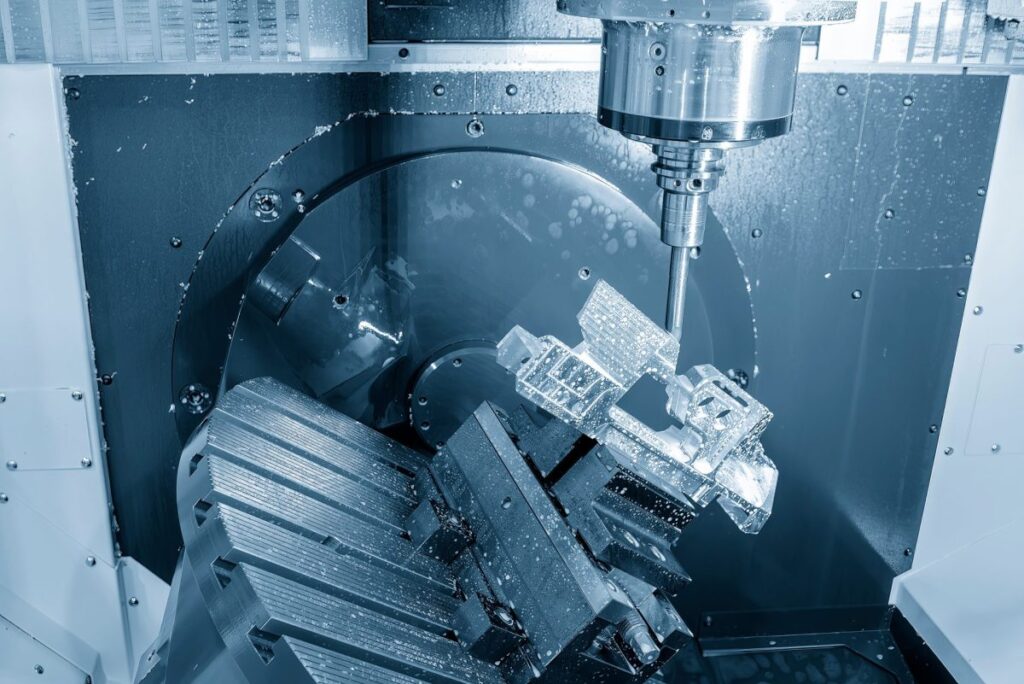
Forging Ahead in the Future of Flight
The aerospace industry’s evolution is linked to advancements in material science. Luxfer MEL Technologies, with its pioneering work on magnesium alloys like Elektron® 21, is at the forefront of this transformation. By embracing innovation, enhancing manufacturing efficiencies, and ensuring material excellence, the company is not just responding to industry challenges—it’s shaping the future of aerospace engineering.
Click Here to view the full article on the IoM3 website (courtesy Materials World March 2024).